

A supra/juxta gingival margin placement is recommended in order to facilitate the tooth exposure and the work field isolation during the optical impression and the luting procedure, respectively. The clinician is not compelled to sub-gingival margin placement, due to the perfect color correspondence between the tooth and the restorative material together with the absence of metal edges. Aesthetics and structural durability are obtained with minimum thickness, since these materials do not require the presence of a metal substructure ( 8). The amount of tooth reduction depends on the achievement of the right thickness for the prosthetic material ( 7). This concept has been supported by continuous introduction of new metal-free adhesive materials, which offer clinical reliability due to enhanced physical and mechanical properties ( 6). The importance of tooth tissue preservation has led to the development of minimal invasive/ultraconservative dentistry. Tooth preparation and milling unit capability The purpose of this paper is to provide a useful evaluation tool, with a detailed description of the system, highlighting and discussing its potential and its limits. However skepticism and a lack of knowledge about this system are still present among clinicians. It should be noticed that almost 30 years have passed since it was born and the rapid advance of the technology over this period have made the devices, the materials as well as the dedicated work protocols more efficient and reliable. To our current knowledge, only limited clinical data about CEREC CAD/CAM chairside system have been reported.
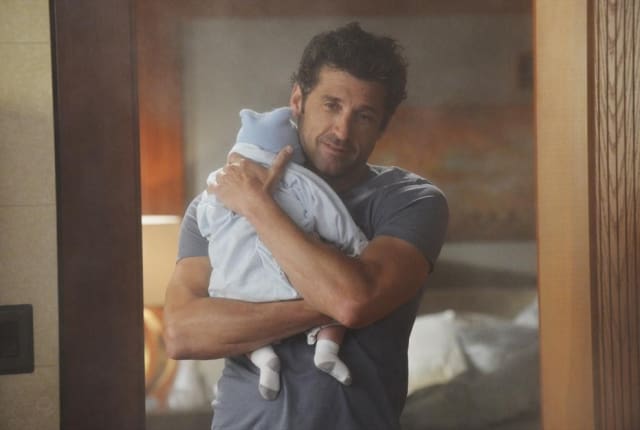
The restoration undergoes a finishing phase (coloring, glazing, polishing) and is then ready for an adhesive luting. The final data are sent to the computer-controlled milling unit (CAM) for a metal-free monoblock milling. Additional features such as the automatic occlusal adjustment, the virtual articulator and the digital smile design (DSD) are provided by the last upgrade.
#Cerec crown reviews software#
The software allows to mark the margins, digitally design virtual wax-up proposals of the restoration, adjust occlusal contacts and calibrate the proximal contact areas. The images of intraorally scanned optical impressions are visualized on the computer monitor in real time and can then be further processed by the clinician interactively (CAD) ( 5).
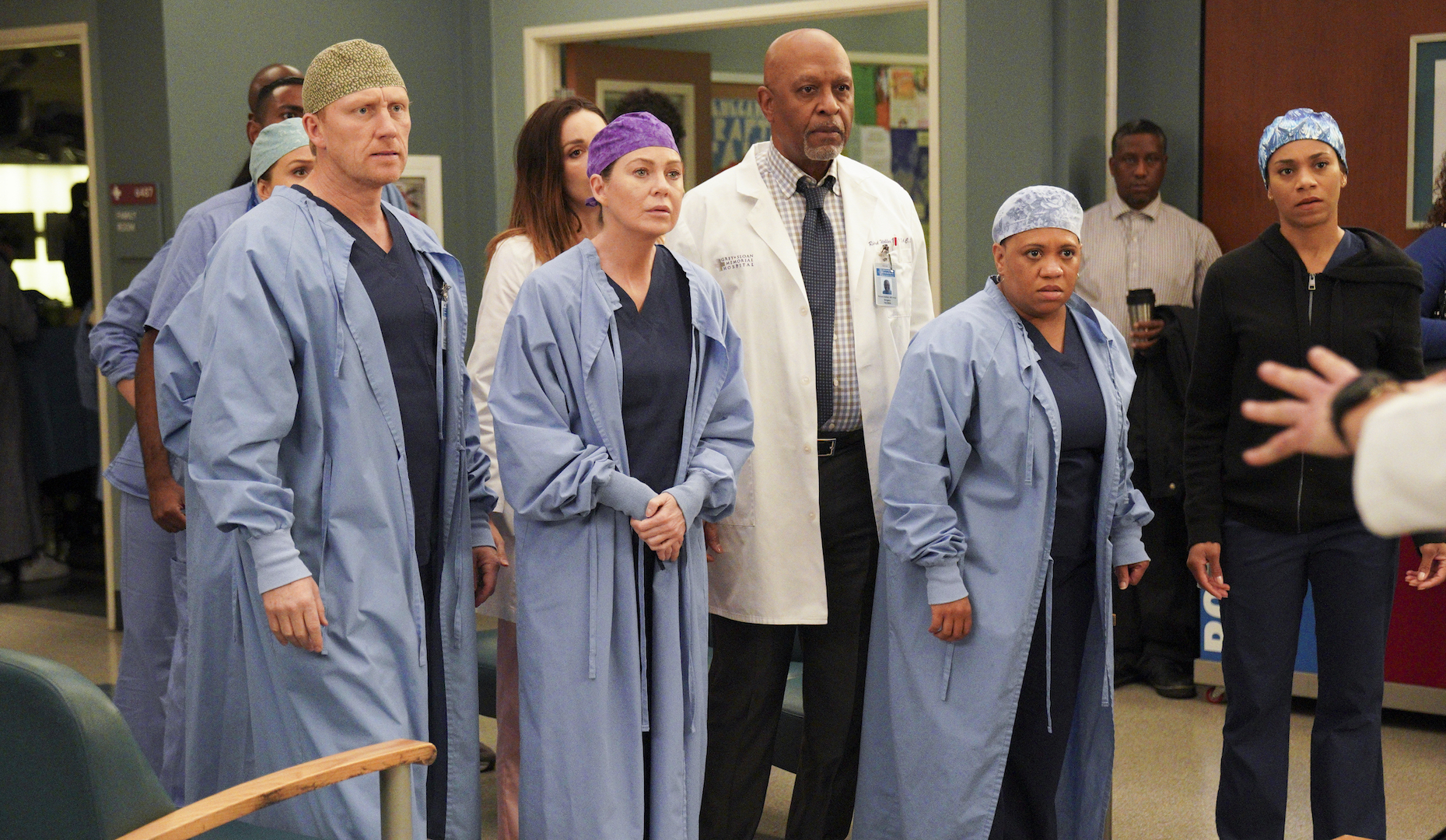
An optical impression is taken by means a scanning device in order to capture complete detail of the teeth and supporting soft-tissue structures ( 4). Modern technologies have improved the system performance, but the workflow was not modified. An immediate feedback on the 3D model during the planning phase has made this technology more intuitive and user friendly, improving quality as well as the clinical work flows of chairside system use.įurthermore the current CEREC 3 system has expanded the restorative capabilities significantly and can fabricate inlays, onlays, veneers, crowns, as well as three unit bridges and custom lithium disilicate implant abutments. The evolution of supportive computer technology over time has led to a three dimensional (3D) design program. The CEREC 1 allowed for a limited 2-dimensional (2-D) view of the scanned images and was able to fabricate exclusively inlays for immediate cementation ( 3).
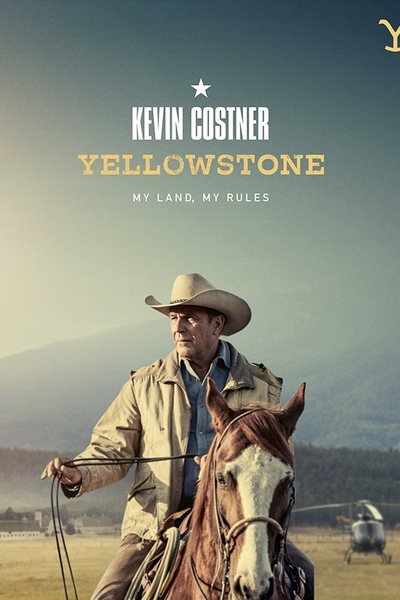
#Cerec crown reviews series#
Since its introduction to the dental field in 1985 as the CEREC 1, this system has evolved through a series of software and hardware upgrades up to the CEREC 3D. This chairside system allows the clinicians in private offices to independently design and also machine dental ceramic restorations in matter of hours, enabling reconstruction during single visit ( 2). The first commercially available CAD/CAM system has been CEREC, developed by Mormann and Brandestini. Nowadays CAD/CAM systems may be categorized as either chairside or laboratory systems.
#Cerec crown reviews manual#
CAD/CAM approach has been introduced in dentistry as a precise, efficient, accurate and error-free tool to produce high-quality dental restorations, as opposed to the traditional way of manual manufacture, which is prone to numerous subjective errors ( 1). The use of computer-aided design computer-aided manufacturing (CAD/CAM) systems in dentistry has increased dramatically during the last decade thanks to the fast development of digital computer technology.
